Leviat Provides Bespoke Approach To Masonry For Impressive Folkestone Development
- dcb1960
- Jan 22
- 2 min read
At Folkestone’s transformative Shoreline development, the creation of a mesmerising brick façade, that forms undulating waves to reflect its coastal location, is a prime example of the way that engineered solutions can bridge the gap between an architect’s vision and the practical engineering requirements. Designed by Acme and built by contractor Jenner for the Folkestone Harbour and Seafront Development Company, Shoreline’s distinctive curved design, featuring convex and concave elements wrapped in a glazed white brick façade, required highly specialised solutions.
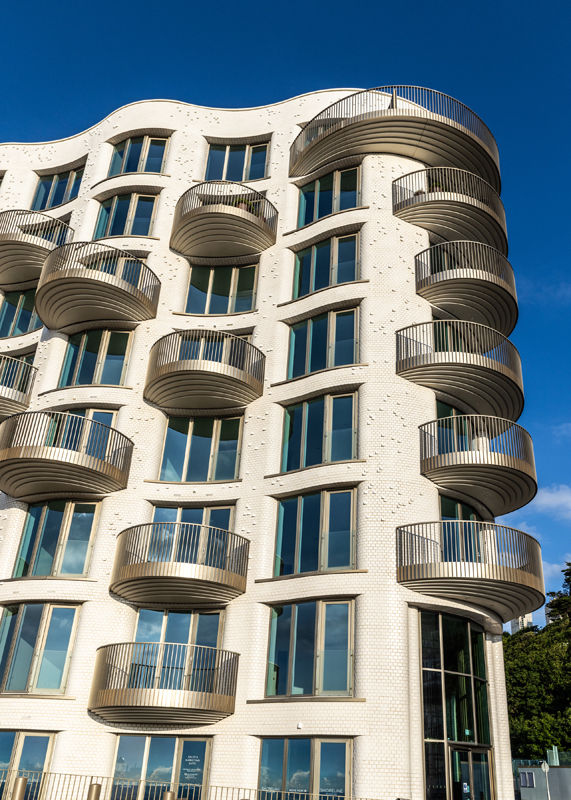
This is where specialist product manufacturers such as Leviat step in, bridging the crucial gap between creative ambition and engineering feasibility. Custom-engineered masonry support systems were crucial to realise the building's complex geometry. Meanwhile, the balcony connections needed innovative non-standard brackets to interface with the curved concrete frame. Collaborating closely with Jenner, Leviat's technical engineers played a pivotal role in delivering support systems that seamlessly integrated into the building's curved design while maintaining an unobtrusive presence. The specification of top-quality materials remained of paramount importance throughout the process.
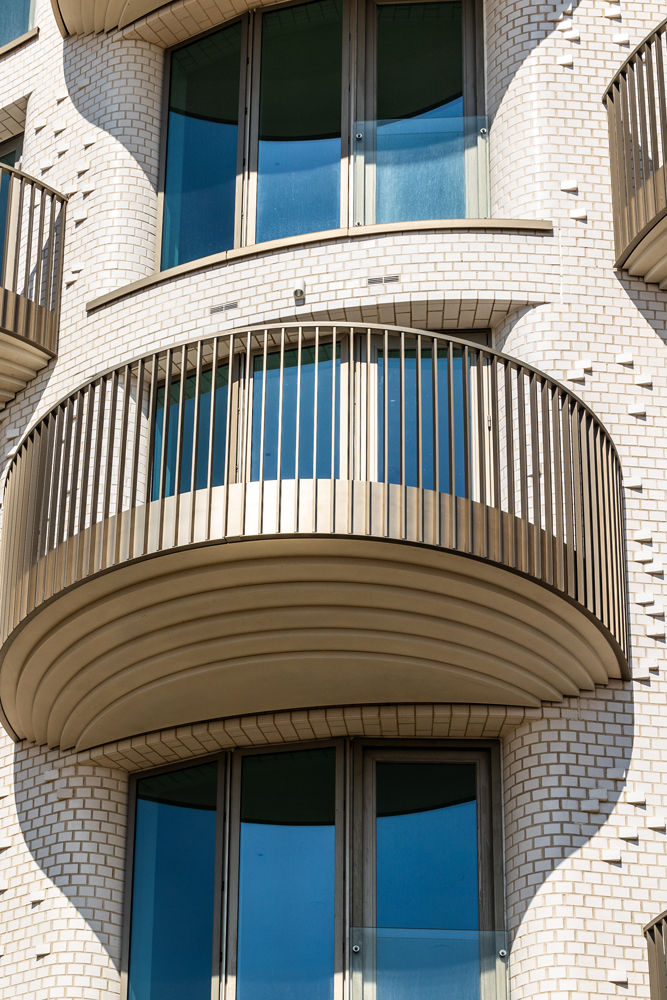
Given the intricate nature of this project where standardised solutions were never going to be an option, early engagement with Leviat was essential. Leviat’s technical engineers, from both the masonry and structural connection teams, worked closely together to deliver engineering solutions that were compatible for both the design and use of Ancon Masonry Support and Ancon Balcony Connectors within the project scheme. These solutions were used across each of the elevations and as part of the brick façades and balconies.
“There were a number of standard balconies across the project but there were also differing sizes and shapes of balconies which necessitated the manufacture of bespoke balcony arms,” said Nobert Omony, Lead Engineer - Structural Connections for Leviat. “This involved designing and manufacturing these brackets for fixing to a curved concrete frame whilst carefully working around the clashes in the reinforcement of that frame.”

What became clear from the Shoreline project is the value of early engagement and close collaboration between the project team and the product manufacturer Leviat to overcome complex design challenges. Leviat’s innovative structural components and technical prowess may be hidden from view but the end result is a structurally sound and visually striking building. www.leviat.com
Comments